Plastic extrusion for large-scale custom plastic parts
Plastic extrusion for large-scale custom plastic parts
Blog Article
Secret Advantages and Considerations of Executing Plastic Extrusion in Your Projects
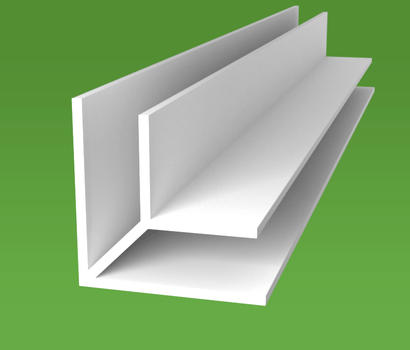
Recognizing the Basics of Plastic Extrusion
Plastic extrusion, a staple in the manufacturing market, is a process that entails melting raw plastic material and reshaping it right into a constant profile. This account, when cooled, can be cut into preferred lengths or curled for later usage. The beauty of plastic extrusion hinges on its flexibility. A broad array of products, from piping to home window frames, can be generated. The procedure calls for an extruder, an intricate equipment with a warmed barrel, a turning screw, and a die at the end. The plastic product, in the kind of pellets, is fed into the extruder, where it's melted and compelled with the die, taking its form. The choice of plastic and the layout of the die establish the item's characteristics.

The Economic Advantage of Plastic Extrusion
The financial advantage of plastic extrusion lies mainly in two locations: cost-efficient material production and advantageous production speeds. With plastic extrusion, businesses can create high volumes of product at a reduced price compared to other techniques. The procedure flaunts a remarkable production speed, considerably reducing time and additional enhancing its financial stability.
Cost-efficient Material Production
A substantial benefit of plastic extrusion is its impressive cost-effectiveness. In addition, the extrusion procedure allows for a high level of accuracy in forming the plastic, decreasing the need for pricey post-production changes or adjustments. All these variables make plastic extrusion a highly economical choice for lots of jobs, supplying an appealing equilibrium in between price and performance.
Beneficial Manufacturing Speeds
While preserving the cost-effectiveness of the products, another notable advantage of plastic extrusion depends on its rapid production rates. This performance in the production procedure is connected to the constant nature of the extrusion procedure, permitting for high-volume production in a reasonably brief time period. The rate of manufacturing straight associates to a decline in labor costs and a boost in outcome, consequently boosting the total financial stability of the process. The busy production does not compromise the high quality of the final item, ensuring constant and dependable outcomes. This mix of speed, cost-effectiveness, and high quality emphasizes the considerable financial benefit of executing plastic extrusion in various tasks.
Flexibility and Personalization: The Staminas of Plastic Extrusion
Among the popular staminas of plastic extrusion hinges on its adaptability and personalization potential. These high qualities unlock to limitless style possibilities, providing suppliers the ability to tailor products to certain demands. This heightened level of personalization not just enhances item functionality yet also considerably boosts product individuality.
Unrestricted Design Possibilities
Plastic extrusion radiates in its capacity to provide nearly endless layout possibilities. This approach supplies flexibility to create intricate shapes and complex accounts, a task hard to achieve with various other fabrication methods. Owing to the liquid nature of molten plastic, the process is flexible enough to generate a varied range of forms, dimensions, and dimensions. The plastic can be controlled to match distinct specs, enabling the manufacturing of personalized geometries and meeting details customer demands. Plastic extrusion can deal with a selection of plastic types, expanding its application extent. This versatile method, for that reason, serves a wide variety of markets from building and construction to automobile, packaging to electronics, and past. With plastic extrusion, the design opportunities are practically countless.
Increasing Item Originality
The flexibility of plastic extrusion can considerably improve product uniqueness. This procedure enables designers to explore different shapes, sizes, and shades, offering them the flexibility to produce distinct products that stick out out there. It is this customization that lends a distinctive identification to every item, differentiating it from its rivals.
In addition to its visual benefits, the customizability of plastic extrusion likewise provides functional advantages. Designers can change go the buildings of the plastic according to the particular requirements of the application, enhancing the item's capability. They can make the plastic more versatile, a lot more long lasting, or more resistant to warmth, depending on what the item requires. Therefore, plastic extrusion not just improves item uniqueness yet additionally its energy and marketability.
Layout Limitations in Plastic Extrusion: What You Need to Know
Exactly how can develop limitations potentially influence the procedure of plastic extrusion? While plastic extrusion is versatile, design constraints can stop its benefits. Particular facility styles might not be feasible due to the restrictions of the extrusion procedure, possibly limiting the development of detailed profiles. The process is less ideal for hollow or multi-chambered structures. Additionally, the extrusion procedure might not constantly offer the desired surface area finish, especially for those requiring high gloss or optical quality. Product selection can likewise position difficulties, as not all polymers appropriate for extrusion. High-temperature immune plastics, for circumstances, might present problems. Understanding these restrictions is crucial for efficient implementation of plastic extrusion in your jobs. plastic extrusion.
Examining the Environmental Impact of Plastic Extrusion
While comprehending layout limitations is a significant facet of plastic extrusion, it is equally crucial to consider its environmental ramifications. The process of plastic extrusion includes melting plastic materials, potentially launching hazardous gases right into the environment. Additionally, the resulting products are typically non-biodegradable, adding to land fill waste. Improvements in modern technology have actually allowed for even more environmentally-friendly techniques. As an example, utilizing recycled plastic products in the extrusion procedure can lower ecological effect. Furthermore, developing naturally degradable plastic alternatives can assist minimize waste concerns. Examining these environmental elements is vital when implementing plastic extrusion projects, ensuring an equilibrium between performance, cost-effectiveness, and ecological obligation.

Situation Research: Successful Projects Making Use Of Plastic Extrusion
Success stories in the area of plastic extrusion abound, showing both the convenience and performance of this manufacturing procedure. One significant instance is the production of PVC pipes utilized in modern-day pipes. This procedure entails melting plastic and forming it into a continual tube, offering considerable cost and durability benefits. Another successful situation is the production of plastic movie for product Bonuses packaging and farming. Through extrusion, makers can create extremely customizable, thin, and robust movies. Automotive industries likewise benefit, using extruded plastic for parts like trim or seals, enhancing lorry durability. These instances highlight plastic extrusion's vital role in various markets, vouching for its adaptability, cost-effectiveness, and trusted result.
Verdict
In conclusion, plastic extrusion uses a reliable and affordable method for producing complex shapes with very little waste. Integrating plastic extrusion right into projects can lead to successful outcomes, as confirmed by many situation research studies.
Plastic extrusion, a staple in the production sector, is a procedure that entails melting raw plastic product and improving it into a constant profile. Plastic extrusion can manage a selection of plastic kinds, broadening its application range.Just how can make limitations potentially affect the process of plastic extrusion? The procedure of plastic extrusion includes melting plastic products, potentially try this website launching harmful gases right into the environment. Making use of recycled plastic products in the extrusion procedure can minimize environmental influence.
Report this page